
Rivet nuts provides a uniform and tight grip around the hole and could probably make a waterproof joint if used in conjunction with sealant.In our tests a M6 (1/4-20) rivet nut spec’d for a 9mm hole worked well for a hole up to ~10mm, but didn’t work well at 11.0mm. They always sit perfectly flush (straight) with the mating surface. We found that rivet nuts have more constant and predictable spinout torque and are less finicky to install.All things considered using a tooth lock washer is more practical, but J-B Weld could be used to lock a spinning cross nut after the fact. This is because it is capable of filling the void (as opposed to CA glue or Loctite that are too thin). J-B weld is the most efficient adhesive and is able to completely prevent a cross nut from spinning.The tooth lock washer also helps the cross nut sit flush and straight with the mating surface. Cross nuts spinout torque is lower and is less predictable, but adding a tooth lock washer under the head completely prevented it from spinning in our test (until bolt damage).(Spinout torque is higher than the recommended tightening torque, and as a result I sheared a bolt during the test.) Rivet nuts have higher spinout resistance, no washer of adhesive are required.
#METAL WELDED RIVET NUTS INSTALL#
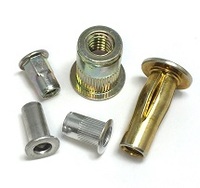
Have to deal with the location of pre-drilled holes.More on that in the Tools & Installation section. Cost more than sheet metal screws or bolts/nuts.

Threaded inserts have the following drawbacks: And as it turns out, many pre-drilled holes in our Ford Transit have blind access so that’s quite convenient. On the other hand, cross nuts and rivet nuts only require access to a single side (front) this is called “blind access”. Installing bolts and nuts requires access from both sides (front and back). Threaded inserts can be used to create joints without having to drill new holes, which would expose bare metal and potentially create corrosion. A van comes from the factory with pre-drilled, unthreaded holes all over the cargo area.
